bulerias1981 - 8-31-2011 at 09:44 AM
Hi all. Wondering if any of you have done repairs on old ouds in which the surface where the bridge is joined to, was not perfectly flat and missing
small chunks of wood.
This oud is old and many parts seem not to be original. The bridge that came with the oud was glued with Gorilla glue, and the bridge was damaged, so
naturally it had to be removed. And also naturally, some small chunks came out when removing the bridge due to gorilla glues immense strength!
A new bridge was made, and glued on. Which after 4 days of string tension, detached from the face. I believe this to be perhaps due to not a perfect
full joint surface, and small crevices from missing small chunks of wood. Other factors could have been humidity or wood fail. I used titebond 3 which
is sufficiently strong.
So my question, whats the best way in your opinion to over come this matter? Should I fill the holes with something, then level it out nice and flat,
then glue the bridge? I don't believe wood filler to be good enough. Perhaps a strong adhesive? Another problem is the top is slightly warped (could
be worse) but the top is a bit concave from years of string tension pulling the face.
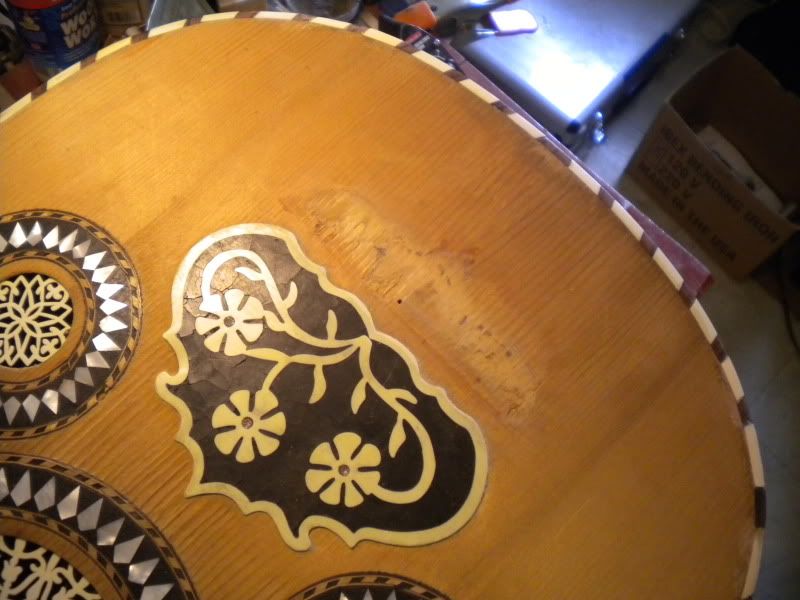

FastForward - 8-31-2011 at 11:38 AM
John, I am no expert but here are my 2 cents,
as you said, if the joint is not well prepared, there is a good change the bridge will detach.
I would recommend putting a medium grit sand paper on top of the face with the grit facing upward and working the bridge slowly to make sure that the
two joints match perfectly. This will take care of any problems due to concavity or warping of the soundboard too.
If you feel that the crevices are causing the face surface to be highly irregular, then I would sand it slightly and try to make it more smooth. I
don't think that filling these crevices with sawdust mixed with hide glue helps at all.
As for glue, I would use hide glue as it is typically recommended for bridges.
Another important thing is to make sure you clean any remaining glue prior to re attaching the bridge.
Ibrahim.
jdowning - 8-31-2011 at 02:37 PM
Gorilla glue (a waterproof, polyurethane foaming glue) no doubt has its applications in general woodworking but gluing instrument bridges is likely
not one of them. The glue joint on a bridge is subject to direct shear stress due to string tension and tensile stress due to bending moment under
string tension. According to Mark Singer, founder of the Gorilla glue company shear strength is not the best feature of polyurethane glues ..... but
that they perform well in gluing end grain where they can migrate up to a depth of 2 inches into the wood (!). Titebond 3 is another type waterproof
glue (PVA). Use of either of these glues may mean that the joint surfaces are now contaminated (i.e. waterproofed) so that the preferred use of hot
hide glue is no longer an option.
Perhaps the only alternative would be to use a hard setting 2 part epoxy cement ('Araldite' is one brand that I have used in the past). With epoxy,
the joint surfaces do not have to be a precise, flat, surface to surface fit as is the case with hot hide glue but can benefit from being 'roughed up'
(for example by cross hatched scoring with a knife blade) to improve joint adhesion. Before gluing with epoxy both joint surfaces must be completely
'degreased' with a suitable solvent such as 'GenClean' or carbon tetrachloride or ether or safer equivalents used in the clothing dry cleaning
industries.
bulerias1981 - 9-1-2011 at 02:10 PM
I think I like the epoxy idea for this case. Thanks for the info.
bulerias1981 - 9-5-2011 at 08:20 AM
jdowning, what is 'GenClean'? Never heard of this.
jdowning - 9-5-2011 at 03:47 PM
It is the trade name for a volatile, non inflammable solvent used to remove grease from clothing - a 'safe' alternative to carbon tetrachloride that
was once used in the dry cleaning industry. Not sure if it is still made but there will be other alternative brands on the market no doubt.
jdowning - 9-6-2011 at 04:47 AM
The spelling should be 'Genklene'.
It is - or was - a version of 111-trichlorethane de-greasing solvent made by the I.C.I. Company. Once available to the general public (1970's) it has
since been banned worldwide (1995) due to greenhouse emissions protocol.
Not sure what other generally available alternatives there might be. Purified gasoline (camping 'gas') might be a possibility. I have used this for
degreasing bone but have not tested it for preparing wood surfaces prior to application of adhesives. It is supposed not to leave any greasy residues
as would standard gasoline but is highly flammable so hazardous to use.